Apprentices – our workforce of tomorrow
Offering apprenticeships is not only a high priority at FISCH®-Tools, it is a tradition. The West Styrian drill factory has been training apprentices for decades. Today, the apprenticeship courses offer young people a future-oriented specialist career with many opportunities and perspectives. We are always looking for young, talented people who want to kick-start their career with the high quality that an apprenticeship offers.
Vocational training – diverse opportunities and perspectives
We offer our apprentices the opportunity to take on more responsibility, learn more and develop their personal skills more than usual. This is how we want to ensure their future professional success!
We have trained more than 150 apprentices in our company in the last 30 years. Every year, several apprentices start their apprenticeship, which alternatively can also be completed with a secondary school certificate (Matura). Around half of the apprentices remain with the company after completing their apprenticeship. With their qualifications, knowledge and experience, they make a significant contribution to the success of the company as specialists.
Would you like to do your apprenticeship in a successful, modern and forward-thinking company? We would love to hear from you!
Apprentices with STAR quality
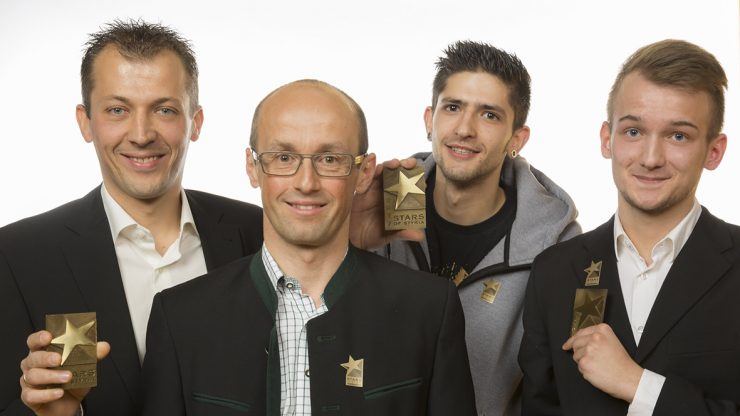
Johann Eberhard GmbH – FISCH®-Tools – has earned an excellent reputation for training outstanding apprentices. Apprentices Matthias Zierer, Philip Rexeis, Philip Kohlbacher and Lisa Fabian who completed their training in our company with great excellent success, received the "Star of Styria" award in recent years at the "Stars of Styria Awards”.
For FISCH®-Tools, "Career with apprenticeship" is much more than just lip service: Since it was founded, the traditional company has invested sustainably in the training of qualified employees and offers top quality Training.
And the success story continues: If you’re enthusiastic about technology and also want to become a "Star of Styria", you can apply for an apprenticeship at FISCH®-Tools at any time at bewerbung@fisch-tools.com We currently offer apprenticeships in the fields of
- metal technology
- precision tool grinding technology
- machining technology
as well as vocational training as an
- office clerk
Office clerk apprenticeship
As an office clerk, you will be responsible for all office-related tasks. This also includes internal communication in addition to office and administration work. You will work with modern hardware and common software tools in order to find solutions to these various tasks.
The versatile and varied activities of office clerks demand a distinct talent for organisation, commercial thinking and the ability to quickly grasp new concepts. Also required are a high level of skill at coping with planning tasks, a high degree of customer orientation as well as knowledge of legal matters and the company’s structures and activities.
A sample of the job and its responsibilities:
• Correspondence – written correspondence and emails
• First point of contact for customers and suppliers
• Organisation of trade fairs and visits to international trade fairs
• Organisation and support of internal and external meetings
• Preparing quotes
• Providing product information over the phone
• Processing orders
• Managing promotional products
• Filing and mail distribution
• etc.
Duration of training: 3 years
Metal technician apprenticeship m/f
A metal technician's responsibilities include a diverse range of tasks: You will use technical documents (blueprints, construction plans) to plan how the work should be completed as well as decide on the equipment and methods required. You procure materials and use hand tools and machines to process them. One of the most important activities in metalworking today is setting up and operating electronically controlled machine tools (CNC machines) and regularly inspecting the finished goods. Other important tasks include assembly, maintenance and repair work on the products as well as surface protection measures.
As a metal technician, you will program and operate computer-aided systems and machines and create design programs and technical drawings with CAD (Computer Aided Design). Parts are processed by means of cutting, bending, milling, turning, welding, etc.
You record and document the technical data of the work processes and results. Maintenance and repair work are also important tasks in metal technology and metalworking technology. You check machines, equipment and devices to make sure they function correctly and also replace worn parts. You oil and lubricate machines and equipment and carry out necessary repair work according to predefined maintenance schedules.
A sample of the job and its responsibilities:
• Planning tasks and deciding on equipment
• Machining materials with hand tools and machines
• Setting up and operating electronically controlled machine tools – CNC machines
• Creating design programmes and technical drawings using CAD
• Machining methods: Cutting, bending, milling, turning, welding, ...
• Collecting and documenting technical data
• Assembly, maintenance and repair work
Duration of training: 3.5 years
Precision tool grinding technician apprenticeship m/f
As a precision tool grinding technician, you will sharpen, maintain and repair highly specialised cutting tools used in computer-controlled machine tools in the highly automated manufacturing industry. Production is also carried out in the companies that manufacture these highly specialised tools. After completing your apprenticeship, you will have a decent knowledge of tool technology and machining technology. Your work also includes programming, setting up and monitoring machine tools as well as having knowledge of tool application and tool management.
The tools and machine tools used today are complex constructions and the grinding and assembling of the tools requires the highest level of accuracy, precision and exact knowledge of the tools’ functions. Maintaining the tools is also an essential task in order to ensure smooth production. The time required to replace, i.e. to remove and install the tools, must be kept to a minimum in order to avoid expensive machine downtimes. The most important tasks and activities in the precision tool grinding technician occupation are therefore the maintenance, restoration and repair of cutting tools; function testing and commissioning cutting tools; programming, setting up and monitoring machine tools; and the manufacture of cutting tools according to customer requirements in individual production.
Before each work order, the precision tool grinding technician first defines the working steps, tools and working methods. You will also regularly draw up records of their work (collection of technical data on the workflow and work results, creation of documentation), carry out quality assurance measures and ensure compliance with quality, safety and environmental standards in the work process.
A sample of the job and its responsibilities:
• Sharpening, maintenance, repair, function testing and commissioning of highly specialised cutting tools
• Gaining specific knowledge of tool technology and cutting technology
• Programming, setting up, monitoring and maintaining machine tools
• Improving your knowledge of tool application and tool management
• Production of cutting tools according to customer requirements in individual production
• Determining and documenting work steps, equipment and working methods
• Quality assurance measures and compliance with quality, safety and environmental standards
Duration of training: 3.5 years
Machining technician apprenticeship m/f
Today, the manufacture of metal components with modern machines and production plants requires not only manual skills but also highly specialised computer knowledge for programming and controlling the systems. Starting with work planning, through production to quality assurance, the skilled workers have to meet high qualification requirements.
As a machining technician, you are responsible for the planning, execution, inspection and manufacture of components with machines and production systems as well as for metal-cutting material processing. To do this, you select the required materials, tools and parts. You procure and inspect them and manufacture machine components on conventional and computer-aided CNC machine tools (Computer Numeric Control). Production processes with conventional machines include filing, sawing, milling, turning, polishing, drilling, countersinking, reaming and thread cutting. However, your activities focus on machining processes with computer-controlled (CNC) machines and production systems. These include drilling, countersinking, reaming, thread cutting, milling, turning and grinding as well as eroding manufacturing processes (spark erosion). You shall create production programs for the CNC machine tools according to the relevant standards. You will also incorporate computer-aided design (CAD) into the production programs and adapt them.
As a machining technician, you equip machine tools and production plants for machining materials, put them into operation, maintain them and carry out maintenance work. If necessary, you systematically search for faults, defects and malfunctions in machine tools and production plants, narrow the problems down and correct them. A machining technician’s areas of responsibility also include the planning and control of work processes, the application of quality management systems and the collection and documentation of technical data about the workflow and results. You will cooperate with colleagues and supervisors and provide feedback on how to optimise design, production and work preparation. Furthermore, you will implement protective measures to prevent personal injury and property damage and check and document them.
A sample of the job and its responsibilities:
• Planning, execution, inspection and production of metal components with modern machines and production facilities as well as metal-cutting material processing
• Application of production processes with conventional machines such as filing, sawing, milling, turning, polishing, drilling, countersinking, reaming and thread cutting
• Creation of production programs for CNC machine tools and computer-aided CAD designs (Computer Aided Design)
• Setting up machine tools and production plants for the machining of materials as well as commissioning, maintenance and repair work
• Planning and monitoring workflows, the application of quality management systems and the collection and documentation of technical data on workflows and results
• Optimisation of design, production and work preparation
• Enforcing protective measures
Duration of training: 3.5 years